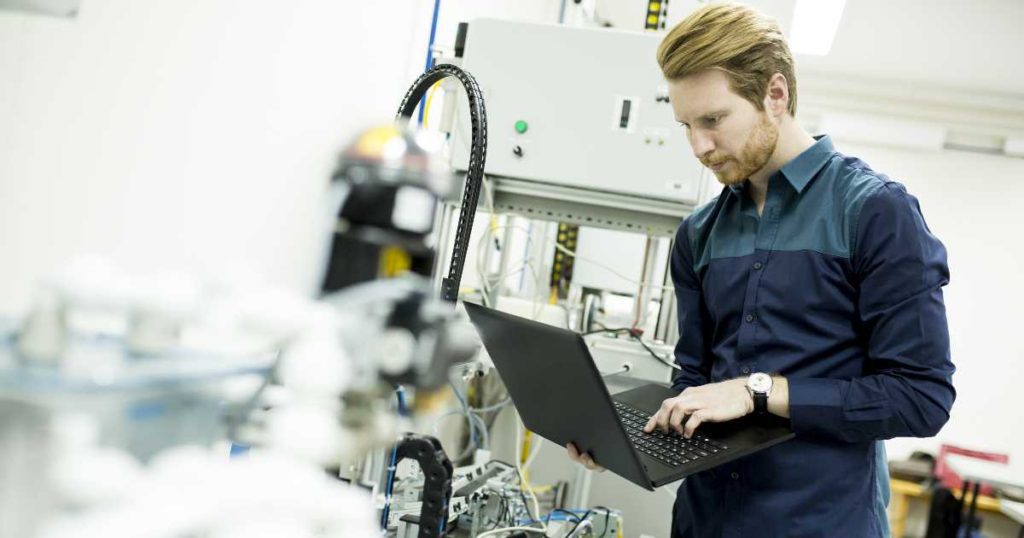
When developing and making a new product, the Bill of Materials (BOM) is one of the most important documents – it is as important as the drawings for the parts, the QC checklists, etc.
If a customer doesn’t have the full BOM information, they really don’t know much about their supply chain and about their product!
Here’s a detailed rundown about what a bill of materials is…
What information is typically included in a BOM?
For each part (i.e. component) that is included in the product & packaging, the Bill Of Materials includes:
- Part number, description, unit, criticality
- Unit price, tooling price, sample price
- Payment terms, delivery terms, lead time, MOQ
- Supplier full contact information
- Supplier approval status
- Specification and/or drawing status
- Quality standard status (approved sample, checklist…)
- Follow up on actions
It may start as an Excel file in the early days of a new product development, and then be imported in an ERP system before parts are purchased. Its structure is relatively standardized.
Here’s part of an example BOM you can see in Excel format:
You can also see a walkthrough of a BOM in this video:
The several types of BOM
A new product development project follows certain phases. The BOM follows these phases and becomes more detailed over time.
Phase 1: the Concept BOM
When defining the general concept of the product, and the specifications at a high level, the team works on the product requirements, on the target time to market, on the target cost, and on the general solution.
A very simple BOM is prepared, with few details if any.
Phase 2: the Design BOM
This is made when the team is defining the specifications in details, including a ‘proof of concept’ if needed. The product specifications and the acceptance requirements are documented, and the general design has been clarified.
A Design BOM is prepared, and it typically includes the key components only.
Phase 3 (prototyping): the Development BOM
The detailed design work is done, and a final prototype is tested and approved.
An Engineering BOM is sufficiently detailed to provide a quotation.
Phases 4 and 5: the Initial Manufacturing BOM
This BOM is made at the time when tooling is made and we undertake pre-production preparation, including a pilot run. It includes the information needed to place orders and manufacture.
Phase 6 (mass production): the Manufacturing BOM
The BOM is a living document and it keeps being updated based on the issues detected, the customer requirements, etc.
The handover from customer to manufacturer
There are mainly 2 cases.
- Case 1: the manufacturer is involved early in the new product design & development, and is asked to prepare the BOM from scratch.
- Case 2: the customer works on the first few phases (often with a design house) and then gives the BOM to the manufacturer, who:
- Reviews it, and may ask for comments or improvements
- Approves it
- Adapts it to its own template
- Keeps adding to it and improving it
In both cases, it is important to understand the customer’s needs & requirements in great detail!
A good understanding of the customer’s needs & requirements is a must
The customer needs to communicate a lot of information, such as:
- Design intent: how the product is to be used, etc.
- Conditions of use: indoor, outdoor, high temperature…
- Appearance requirements: strict acceptance criteria have an impact on the type of suppliers to pick.
- Special requirements: for example, if materials need to be fire retardant, this needs to be known from the start.
Reviews and approvals
Making a mistake in the BOM can have severe consequences (very expensive for the manufacturer). There are 3 cases:
- A very simple BOM prepared by an experienced project manager (PM) at the concept or design phase doesn’t need to be reviewed. That PM can approve it.
- Otherwise, the BOM must be reviewed by a person or a team (R&D, purchasing, quality, production…) that can detect most issues.
- For complex BOMs, several rounds of reviews may be necessary before approval.
- If a customer drafts the BOM, the manufacturer still needs to review & approve it.
The general flow is as follows:
PM drafts > Review > List of issues > PM fixes issues > Review, no issue > Approval
Document control best practices
Using an out-of-date version of the BOM can also have severe consequences.
- When a PM starts to draft a BOM, always take the latest template on a shared server
- We need to know who drafted the BOM, who reviewed it, who approved it. And when these actions took place. It must be obvious and follow the usual procedure for controlled documents.
- The latest approved version must be available in a secure place where other people working on the project can find it.
- The manufacturing BOM can be updated, following the Engineering Change Request procedure.
Confidentiality issues
The BOM includes the list of component suppliers, the prices, etc. and that is all part of the information that must never be sent to other parties. If it spread, it could hurt the customer very badly.
It is all very confidential!
Get your manufacturing project started!
Unsure where to get started with your new product development and/or production? Contact our manufacturing experts to confidentially discuss your situation and see how and where we can assist you with the design, development, manufacturing, and more.

About Renaud Anjoran
Renaud is a recognised expert in quality, reliability, and supply chain issues and is Agilian's Executive VP. He has decades of experience in electronics, textiles, plastic injection, die casting, eyewear, furniture, oil & gas, and paint. He is also an ASQ-Certified ‘Quality Engineer’, ‘Reliability Engineer’, and ‘Quality Manager’, and a certified ISO 9001, 13485, and 14001 Lead Auditor.