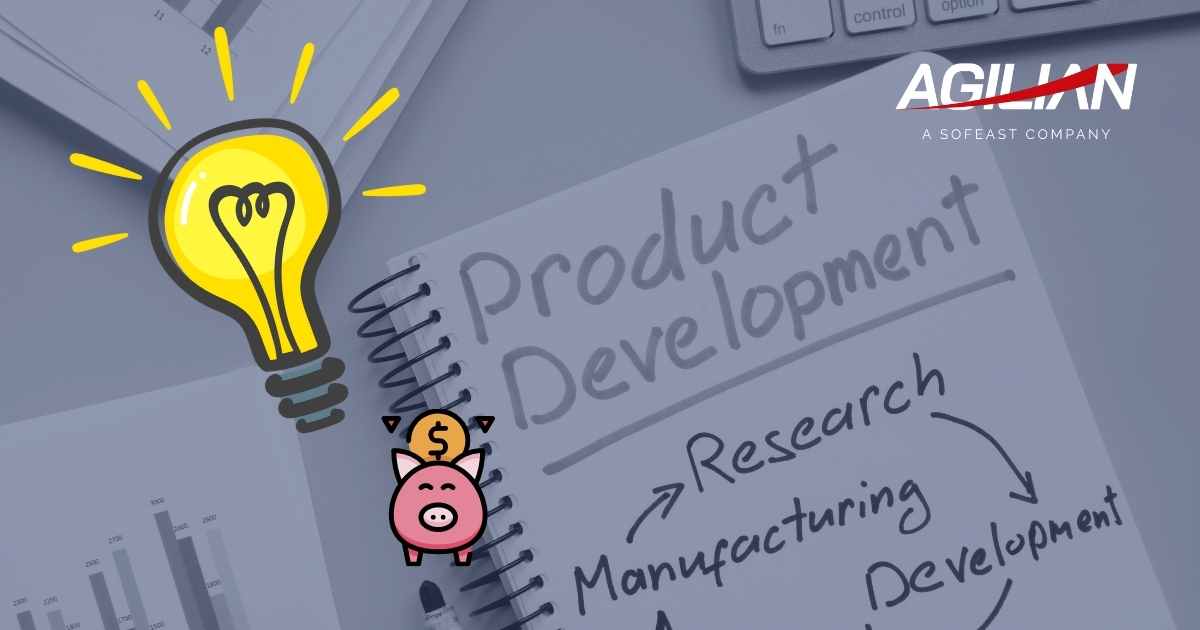
Let’s look at how to reduce the product development lifecycle time and the benefits of doing so to importers who’re developing and manufacturing a new product.
What is the lifecycle time when developing new products?
The product development lifecycle is basically how long it takes to produce a new product from start to finish. For some products it might take about a year and a half in total, for example, but how do we come to that timescale?
The year and a half timescale would be divided into design and development phases before the product finally goes to production where every team involved know what they’re supposed to be doing. Then, depending on what kind of product they’re making, they divide the timing of each stage into mini sections, and in each section they determine roughly how long it takes to do one prototype build and then take that one build and test and validate it to make sure that it meets certain goals and requirements and then fix a few issues and go and do another build including the improvements, and so on. Most companies basically do these iterations of fixes until the NPI new product development phases are completed, and now you’re ready for production.
We made a good illustration of the product development lifecycle and the many activities included that assure that a product goes into production with the minimum of quality, reliability, and compliance risks:
You can learn more about the NPI process and the phases it includes here: The NPI Process You Need To Follow For Successful Manufacturing
How long is the lifecycle likely to be?
As you can see in the graphic earlier, there is a lot to do if we focus on bringing a product to market that reaches our quality standard and customers’ expectations. The whole period could be anywhere from three months to a year and a half. A typical consumer product life cycle time, we’re talking laptops, mobile phones, tape recorders, battery banks, etc, is usually anywhere from around two to three up to six months for the product engineering development life cycle and then the product goes into production and is shipped to customers.
Why to reduce the lifecycle time?
Why do we really care about reducing the product development lifecycle time?
It takes a lot of money to hire a team of people to spend time designing and developing one product. If you’re able to shave some time off the lifecycle for one product it may be possible to manufacture two at the same time as the team can work on a second. That’s a lot better value for money for your business.
How to reduce the time taken during product development?
The typical development life cycle is divided into EVT, DVT, and PVT and there are always opportunities to reduce the time taken during these phases. For example, I used to work in companies where we did three EVT and DVT builds and then one or two PVT builds. Each one of these builds took between two weeks to a month, so that equals around three to six months spent just trying to get the product to production.
So, rather than multiple builds per phase, the question is how can you do one EVT build and then move to DVT right after? If that’s possible, you have saved doing two EVT builds which means you have saved on time and resource expenses and have sped up the time to market by months, too.
Here’s what your product needs in order to reduce the time:
- A robust design
Your design needs to incorporate design for X optimizations such as quality, reliability, manufacturability, etc. By having a robust design you are already reducing the time to market because you’re building a well-designed product which achieves your goals earlier and has fewer issues to put right during testing and validation of prototype builds. - Quality components and suppliers
You have to source suppliers who are capable of providing quality components and assure that each component for your design goes through validation of the performance, quality, and reliability, and then make sure that your design is tested by doing a pilot run with the new component so you don’t have any issues in the field later. - Optimal testing
Be sure that you have an optimal reliability test plan and that your product is tested for various environments as well as worst-case user scenarios. You also need to test the software thoroughly if the product has it.
A good example of testing would be performing a drop test for mobile phones. You know that the majority of your customers will most likely drop their phone at some point, so you want to make sure that you cover issues that could come such as a phone breaking immediately when dropped from a very low height of less than one meter.
Building a quality product including all three of these attributes is one effective way to reduce issues going into a production build and get to market faster because it should result in fewer fixes and the ability to reduce the number of prototype builds you make. If you have successfully implemented these three processes, most of the time there is no need to go through several EVT, DVT, and PVT builds and you can most likely go from EVT-1 directly to DVT-1 and then PVT-1, because as soon as your prototype seems to be solid you can start doing production testing and test it to user scenarios, basically treating the product design as if it’s almost finished.
The product type has an impact on the speed you can go through the product development lifecycle, though. Some products are pretty simple, so maybe you only need a couple of weeks for EVT, whereas more sophisticated products may require a few months. But a typically achievable EVT time period for products that incorporate good design, components, and testing should be between two weeks to a month and a half for many consumer products including electronics. If that’s the case, you have already saved at least two to three months by not moving into EVT-2 and EVT-3.
When you move into DVT you do exactly the same type of cookie cut process and you can end up saving another two to three months, and again, the same in PVT, too. For total time saved we’re talking about anywhere from six to nine months, not to mention the savings on resources, materials, and so on for building the many sample prototypes used for testing in each build. Time is valuable, but the cost saving on materials and components could be a tremendous amount of money when you think about, for example, how much each PCB costs each time you have to build, say, 100 units. A six to nine-month shorter product development life cycle could go up to millions of dollars of savings!
Benefits of reducing your lifecycle time
Let’s break down some of the key benefits you’ll gain from shortening the development lifecycle:
- Financial savings – as mentioned, this could be an enormous amount of money allowing you to price your product lower and blow away your competitors’ costs, or simply make more profit per unit.
- Quicker time to market – you can fulfill orders that have been promised, for example guaranteeing that the product gets on the shelves in time for Christmas, because a longer development life cycle can put delivery dates at risk.
- Enhanced customer satisfaction – if you’ve announced that new products are coming soon and people are excited and then you have to delay them, so hitting launch targets and being able to provide better pricing can provide happier customers.
Milestone reviews for security
One risk you must be aware of is not cutting too many corners in the eagerness to go quickly from EVT to DVT. This could open you up to all kinds of quality and reliability issues in production that simply weren’t caught by testing, so be sure to implement milestone reviews before moving forwards. They’re where the heads of all the departments get together and discuss all the issues they have faced with the design so far and examine the risks, DFM and DFA, and also the FMEA and determine whether or not there are any reasons why they shouldn’t move ahead from EVT to DVT. If even one major risk is found it’s best not to take a chance and go from EVT-1 to EVT-2 in order to figure out the issue/s and fix it before going into DVT.
Conclusion
You’ve now seen, in a nutshell, how you can save time, resources, and costs by reducing the product development life cycle time. Assuring that you use good design, components, and testing is a must.
So in conclusion, you can definitely save a lot of time, speed up the time to market, and save millions of dollars in some cases by shortening the product development lifecycle as long as you don’t cut corners on quality and reliability!
Get help to bring your new product to market faster!
At Agilian, we take control of your new product development and production project locally. The repeatable NPI process we follow includes all of the product qualification steps mentioned here, so you have the best chance of getting into mass production with as few risks of product issues as possible. We communicate in plain English what we’re going to do if you don’t approve, we don’t do it. If you do, we implement the NPI process stages and give you the results, as well as our opinions and recommendations at each stage.
The key ingredient for success is milestone reviews where our project and program managers go through every one of these stages’ results methodically before we move on to the next stage for you, so nothing is missed. This is particularly helpful for businesses who want to gain the benefits of manufacturing in China, but cannot come to the country easily/at all for hands-on involvement in their new product’s development and mass production.
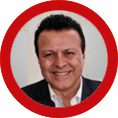