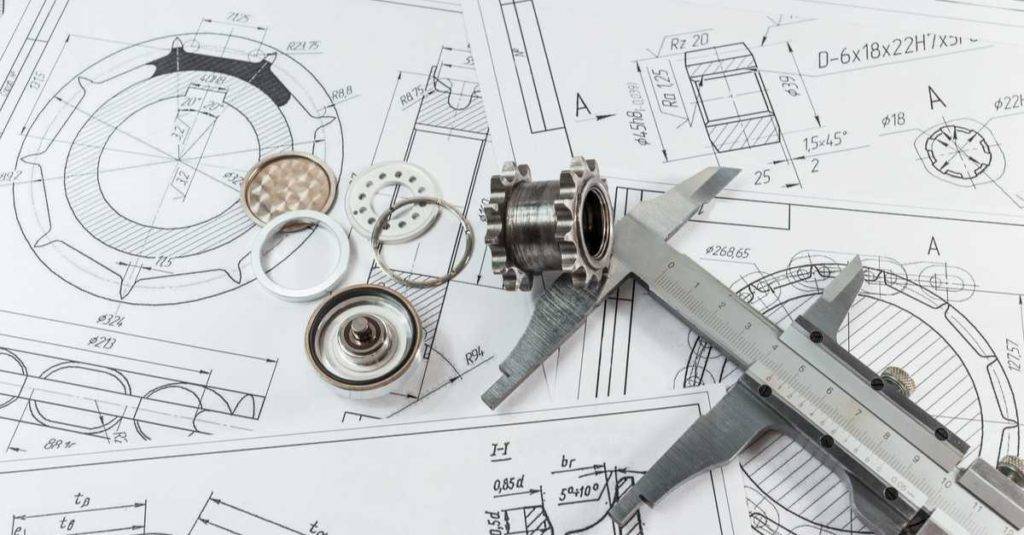
Have you been working on the design of a new product? Maybe you are in the prototyping phase, you are discussing with suppliers, you are starting to think of important quality criteria… If so, you should try and make good use of 2D drawings as they will help you communicate what is important.
Read on for 6 ways in which 2D drawings can improve communication throughout the product development and manufacturing process.
6 ways that 2D drawings help communication
Let me start by saying that 3D drawings are what really matters, but here the point is, not everybody will take the time to open 3D drawings and read all the details. For certain purposes, simpler is better.
1. 2D drawings contain basic information
The BOM can include some of this information, but 2D drawings are in graphical form and are usually easier to read & understand.
Here are a few examples of information:
- Shape and dimensions
- Material
- Color
2. 2D drawings contain information that is very important for quality purposes
Make sure the specifications of each of those parts (especially custom-designed parts) are clear to all involved parties. Clear communication on requirements tends to prevent misunderstandings, which are a major source of quality issues in China.
The documents should contain these, among others:
- Tolerances on dimensions
- Special requirements (surface finishing, hardness, tests the part needs to pass…)
- In case there are many requirements, make sure the ‘critical to quality’ (CTQ) ones are clear and can’t be missed
3. Purchasers and component suppliers need that information
Small and not-very-organized Chinese manufacturers may not have the patience to read through pages of specifications. They need to have all the information in graphical form, as much as practical.
(Note: As we mentioned before, a feasibility study often includes asking for information and confirmations from suppliers – that’s the time to get feedback on the drawings and associated quality specifications.)
4. Incoming QC inspectors need that information
Having all the important information on the drawing makes IQC staff’s work much easier. If they still don’t understand something, they can call the design engineer, and discussing troublesome points by referring to the drawing is pretty much always the most convenient approach.
They can check what is ‘CTQ’ on a higher sampling and in more detail. It allows them to catch serious issues while making good use of their time.
(Note: they should still use approved samples to confirm the general touch & feel, of course.)
5. The whole organization needs to be on the same page
Documenting the quality standard and keeping it up to date is not just a good practice – it really is a must.
The mechanical engineer responsible for the part drawing simply keeps updating the 2D drawings, and the latest version is systematically pushed to the rest of the organization. That’s basic document control. It reduces confusion as well as back-and-forth communication, and it prevents mistakes.
6. Customers need to be able to understand how the parts are designed, too
At Agilian, we hold firmly the conviction that customers need to fully ‘own’ their product as well as their supply chain.
It implies, among other things, that they should have all the drawing files in native format. And, in case they are not technically inclined, they will be more likely to study and approve 2D rather than 3D drawings. Again, all this is a very good thing for communication.
Get involved!
Do you have any questions about this topic or experiences to share? Maybe you need help with your product development? Please leave us a comment or hit the button to contact us:

About Renaud Anjoran
Renaud is a recognised expert in quality, reliability, and supply chain issues and is Agilian's Executive VP. He has decades of experience in electronics, textiles, plastic injection, die casting, eyewear, furniture, oil & gas, and paint. He is also an ASQ-Certified ‘Quality Engineer’, ‘Reliability Engineer’, and ‘Quality Manager’, and a certified ISO 9001, 13485, and 14001 Lead Auditor.