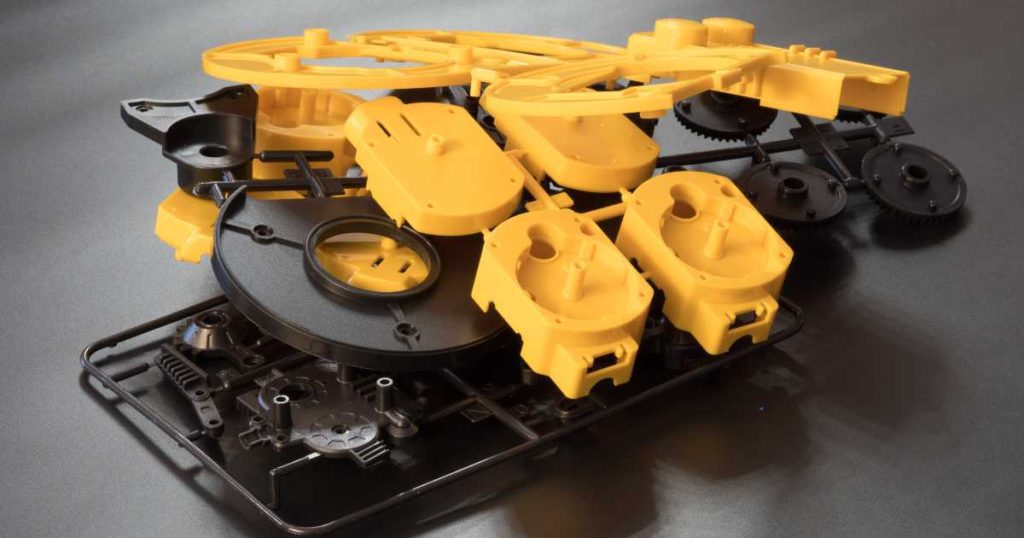
How do you ensure your design is mature, and you are ready to order the fabrication of the mold for your new injection molded plastic part? One way is to carry out a Design for Manufacture (DFM) analysis.
This way, most potential issues will be raised and you can generate a correct action list to eradicate any potential issue before it occurs.
Breaking down the Design For Manufacture (DFM) analysis
The DFM analysis can be broken down into different elements to make it easier to focus on specific issues and actions. Let’s have a look at some of the most common DFM improvements for your plastic injection molded parts:
Design for Quality (DFQ)
- Assembly problems – impossible to assemble or disassemble
- Surface aspects due to injection molding process – sink marks and other imperfections
- Structure weakness – ensure your have the correct radii at intersections, correct section change thickness ratios
- Mechanical simulation weakness like gears, bending arms – this can be analyzed with software simulation of stresses and loads
- Deformed parts due to shape – software simulation will be able to analyze your part to indicate potential issues in the design from this perspective
- Reduce vibration with optimized join position – vibration and harmonics can be a serious issue depending upon your product, make sure you understand the implications of this
Design for Cost (DFC)
- Press fit instead of screws – reduces part count and assembly time
- Simplify assembly with fewer parts – combine multiple parts into a single design wherever possible
- Select the right plastic or process for the purpose – correct material selection is paramount in every product design; ensure you understand the attributes your product needs to have so that the material selection can be based upon the correct properties of the polymer
- Modify the parts to use a better or cheaper process – keep it simple wherever possible, this will help reduce the overall part cost
Design for Manufacture (DFM)
- Draft angles on walls for unmolding – parts sticking in the mold slows the production time and damages parts during the ejection stage
- Ensure injection material flow to get consistent material density – this can be checked with mold flow analysis software; correct cavity fill and cooling are key aspects to every injection mold job
- Simplify the structure to reduce the number of sliders and increase the cavities – don’t make the part unnecessarily complicated just for the sake of it, ‘keep it simple where possible’ is always the best policy
- Add features for ultrasonic welding – welding parts together saves on time, on additional parts, and also reduces errors during assembly; can also provide other benefits (e.g. waterproof)
- Magnetic screws – if you need to use screws to assemble your product, specify screws that can be used with magnetic drivers
These are just some of the elements that can help improve your injection molded part through the use of the Design for Manufacture reviews during the product design phase.
Check out our article on QualityInspection.org for even more information about how to avoid plastic injection molding defects.
Any questions about DFM?
Please leave a comment with your questions or thoughts about design for manufacture and any issues you may have with plastic injection molded parts or products. You can also hit the button to ask us a question and we’ll be happy to respond.

About Renaud Anjoran
Renaud is a recognised expert in quality, reliability, and supply chain issues and is Agilian's Executive VP. He has decades of experience in electronics, textiles, plastic injection, die casting, eyewear, furniture, oil & gas, and paint. He is also an ASQ-Certified ‘Quality Engineer’, ‘Reliability Engineer’, and ‘Quality Manager’, and a certified ISO 9001, 13485, and 14001 Lead Auditor.