PCBA (Surface Mount Technology)
When our electronic engineers need to make a few prototype boards, they can quickly get them through our prototyping PCBA equipment (solder paste printing, SMT pick & place robot, and mini oven). Suitable for up to about 100 boards.
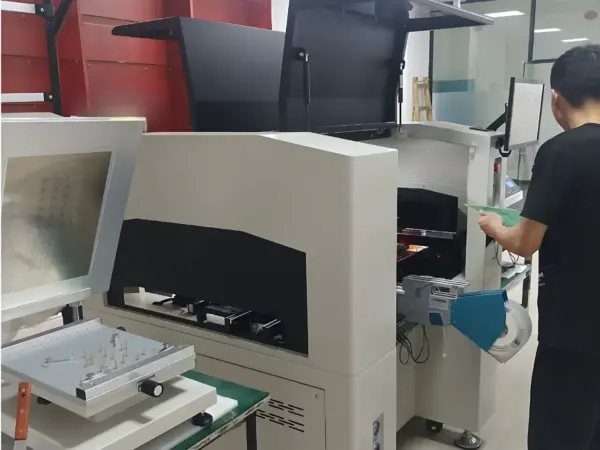